Case Study
Utility Plant Upgrades for Enhanced Operational Efficiency
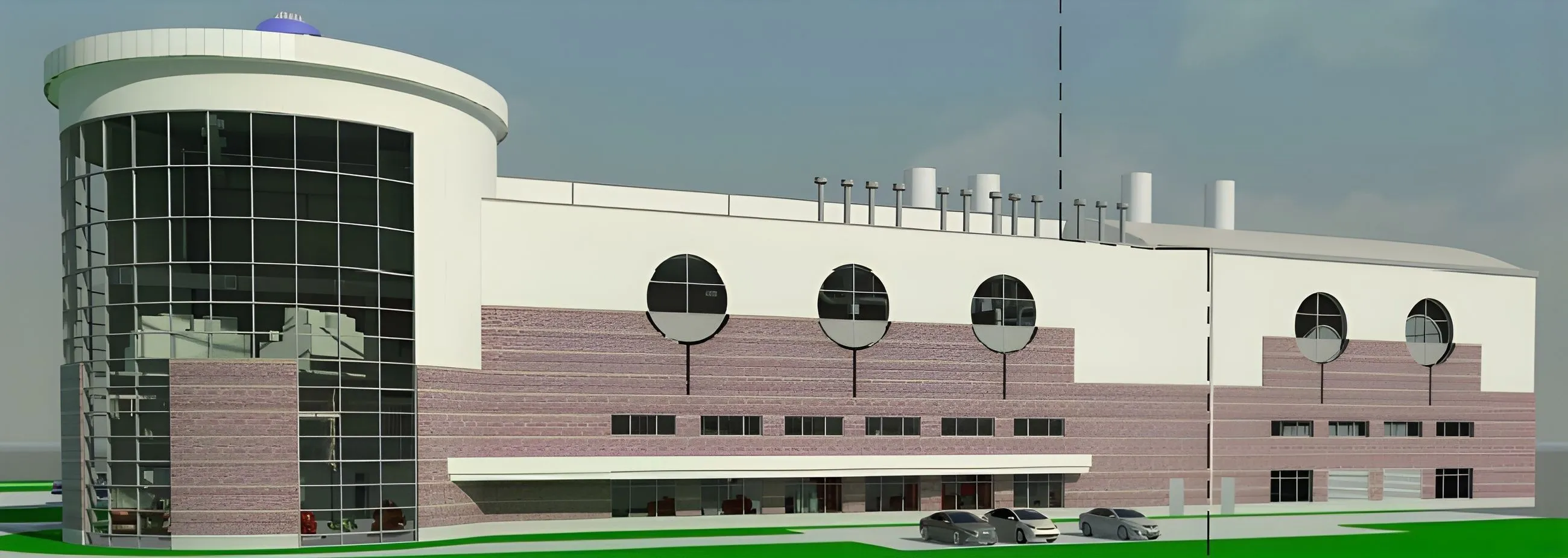
Introduction
BSI Engineering partnered with an engine manufacturing facility to perform comprehensive utility plant upgrades, addressing inefficiencies in aging systems and increasing operational reliability. This project aimed to modernize critical infrastructure, reduce energy costs, and support growing production demands.
The result was a fully optimized utility plant that delivered enhanced performance, reliability, and cost savings, reinforcing the facility’s ability to meet production goals efficiently.
Discovery
The client’s utility plant faced challenges with outdated equipment, inconsistent performance, and high energy costs. Chillers, boilers, air compressors, and cooling towers were operating inefficiently, while the plant’s water treatment and power systems required modernization to support increased production capacity.
BSI Engineering conducted a detailed assessment of the plant, engaging with the client to identify operational bottlenecks and prioritize upgrades. The findings revealed the need for equipment replacements, system redesigns, and improved utility distribution to ensure long-term operational efficiency.
Research
BSI Engineering conducted thorough evaluations to address these issues:
- System Diagnostics: Verified equipment sizing for chillers, boilers, and air compressors to identify bottlenecks.
- Energy Efficiency Analysis: Assessed energy usage patterns to pinpoint areas for cost savings.
- Water and Steam Systems: Studied the reverse osmosis system and steam generation requirements for optimal performance.
Planning
A comprehensive upgrade plan was developed to align with the client’s goals. This included replacing aging chillers, boilers, and cooling towers with energy-efficient models, redesigning site-wide piping for water and steam distribution, and modernizing electrical systems to support harmonics and power efficiency.
Detailed designs were created for the new control room and engineering office to enhance system monitoring and management. A phased implementation plan was adopted to minimize disruptions to ongoing operations, with a clear focus on maintaining production schedules throughout the upgrade process.
Delivery
BSI Engineering implemented the upgrades efficiently and on schedule:
- Utility Systems: Installed advanced chillers, boilers, and air compressors, improving energy efficiency and capacity.
- Water Treatment: Designed a reverse osmosis system for better water quality and reduced waste.
- Electrical Upgrades: Modernized power systems and implemented controls to optimize energy usage.
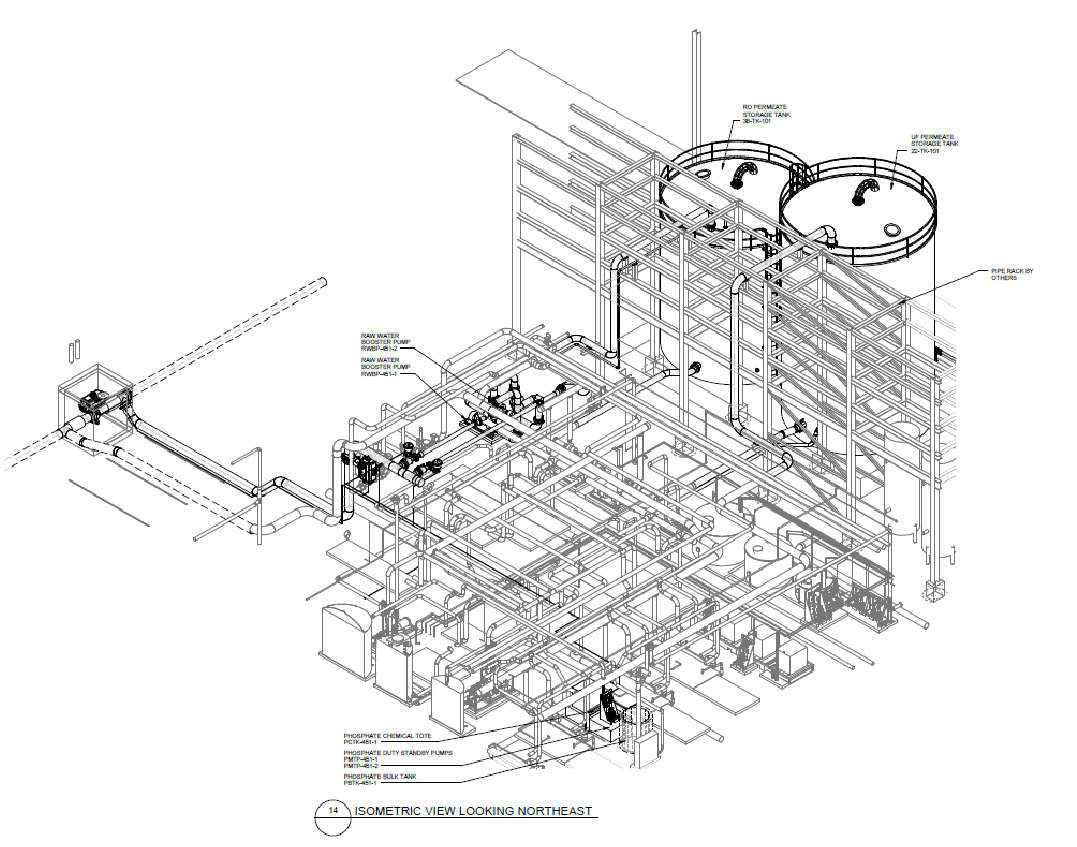
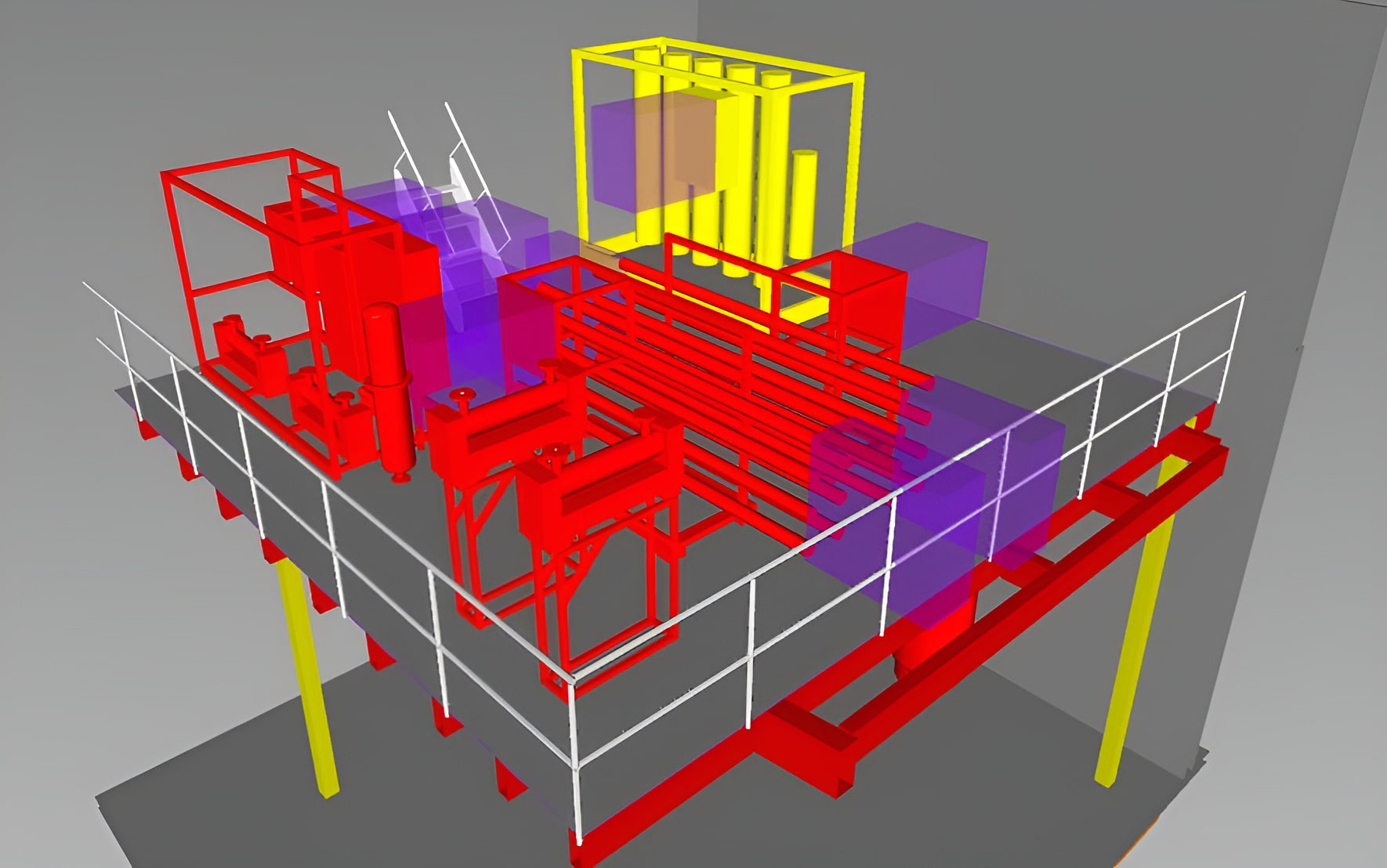
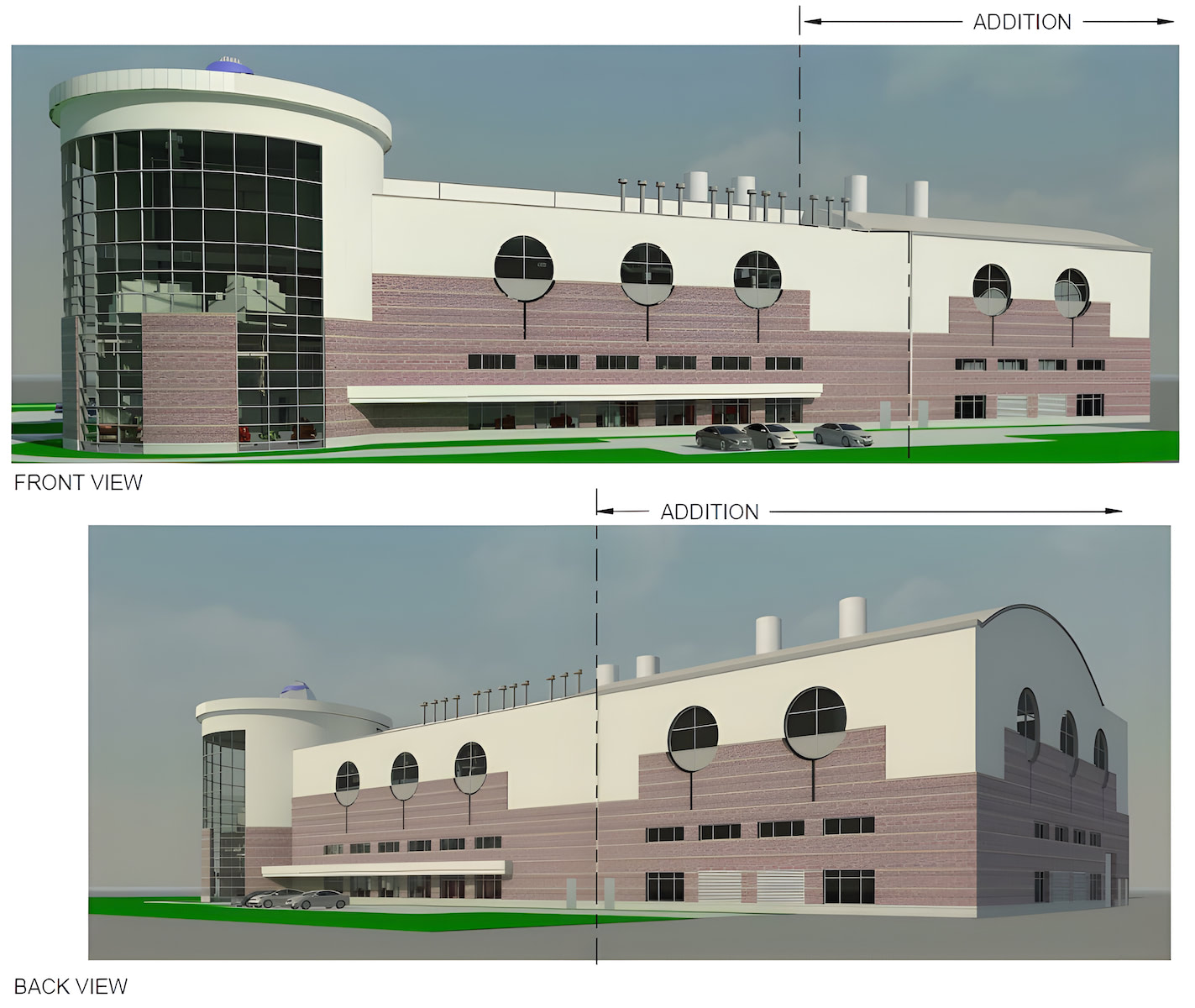
Results
Results
The utility plant upgrades delivered substantial benefits for the client. Energy costs were reduced by 25% through the implementation of efficient systems, while overall utility capacity increased by 20%, enabling the facility to support higher production volumes. System reliability was greatly enhanced, reducing downtime and maintenance costs.
These improvements positioned the client for sustained operational efficiency and future scalability, demonstrating the value of BSI Engineering’s expertise in utility plant optimization.
Decrease in energy costs from upgraded systems.
Compliance with updated safety and operational standards.
Increase in utility capacity to meet growing production demands.
Other Projects
Read more success stories
Contact
Ready to transform your vision into reality?
Contact BSI Engineering today to discuss your project needs. Our team of over 250 engineers and designers across 4 Midwest offices is ready to serve you.