Case Study
Transforming Aviation Testing Facilities for Enhanced Performance
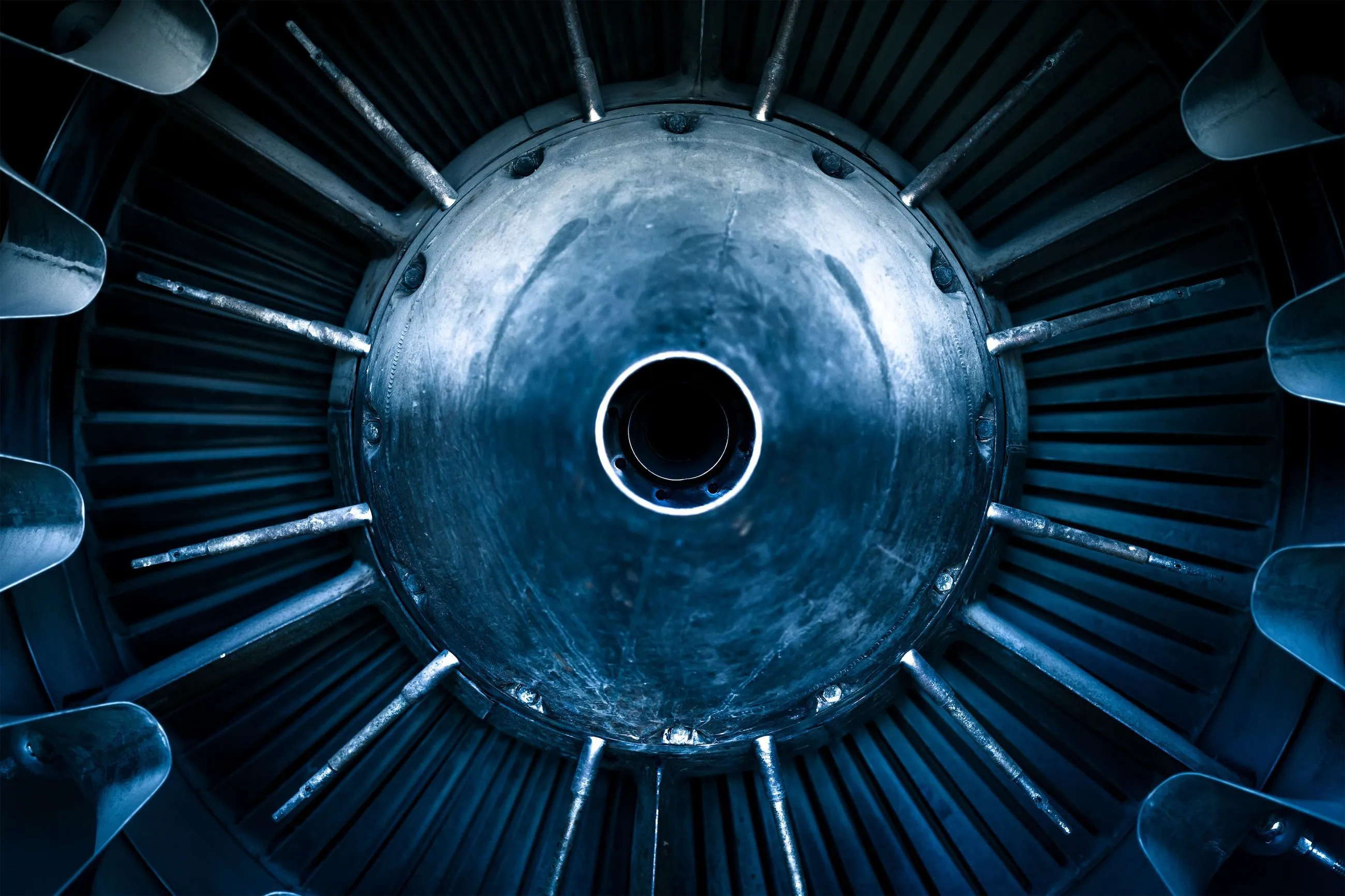
Introduction
In an industry where precision and reliability are paramount, BSI Engineering partnered with two leading turbine manufacturers to design and construct cutting-edge combustor test cells. These facilities were engineered to meet the rigorous demands of testing gas turbine combustors under extreme conditions. By combining advanced technology and innovative engineering solutions, the project enabled the aviation sector to conduct more precise and efficient testing, ensuring optimal turbine performance.
This project underscored BSI Engineering's expertise in delivering specialized solutions for complex challenges, creating facilities that not only met but exceeded the expectations of the aviation industry.
Discovery
The aviation sector faces relentless pressure to improve the performance and reliability of gas turbines. Manufacturers recognized a gap in their existing infrastructure, which struggled to accommodate testing for modern combustor designs. The need for facilities capable of handling high combustion airflows at elevated temperatures and pressures became apparent.
BSI Engineering engaged with stakeholders to thoroughly understand their operational needs. The manufacturers emphasized the importance of precision in replicating operational conditions, requiring robust designs for both airflow systems and safety mechanisms. This discovery phase set the foundation for a tailored solution that would address current limitations while preparing for future advancements in turbine technology.
Research
To ensure the new facilities met the exacting requirements, BSI Engineering conducted comprehensive research into existing test cell technologies and their limitations. The team analyzed global benchmarks in combustor testing and collaborated with industry experts to identify the latest innovations in material science, thermal dynamics, and safety protocols.
Simultaneously, an in-depth assessment of client-specific needs was undertaken. Factors such as airflow volume, temperature control, and real-time data acquisition were studied to create a design blueprint. The research phase culminated in the selection of advanced materials and systems that would support the high-stakes testing environment required by turbine manufacturers.
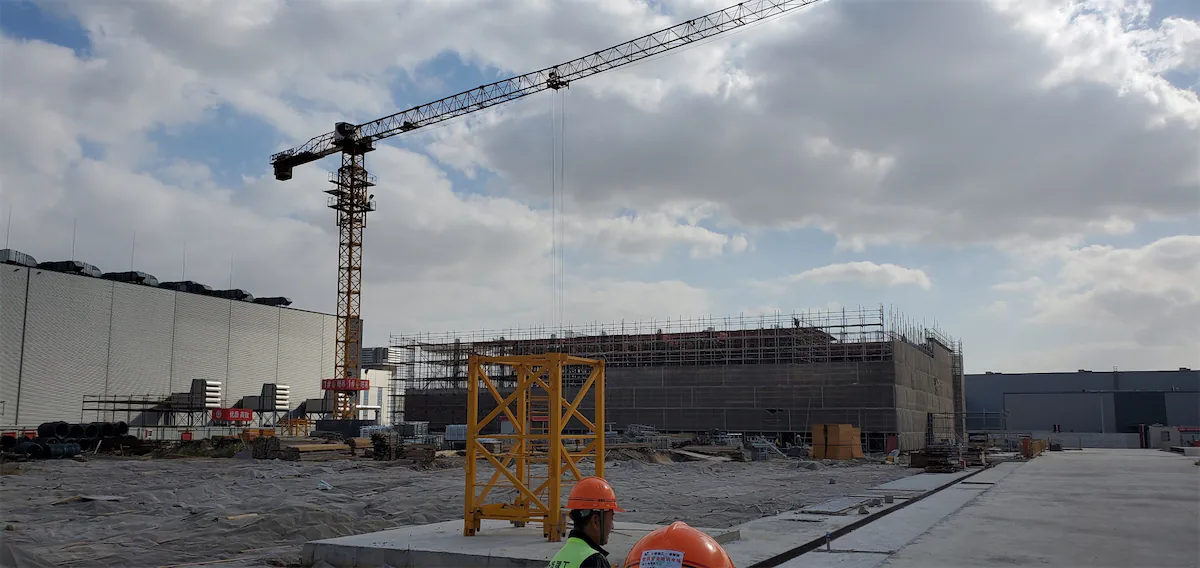
Planning
BSI Engineering's planning process involved close collaboration with the client to translate research findings into actionable designs. The team developed a comprehensive plan for the two combustor test cells, each tailored to meet specific operational goals. The first facility was designed to deliver 75 kg/s of combustion air at 1100K and 5.5 MPa, while the second featured capacities of 120 lb/s at 1500°F and 1000 psia.
Extensive engineering models were created to ensure seamless integration of these systems into the facilities. Detailed schematics for high temperature alloy equipment, pipe supports, structural steel, instrumentation and control systems, and electrical systems were drawn up, with a focus on precision and durability. By incorporating client feedback throughout the planning phase, BSI Engineering ensured the project would align with their operational and safety expectations.
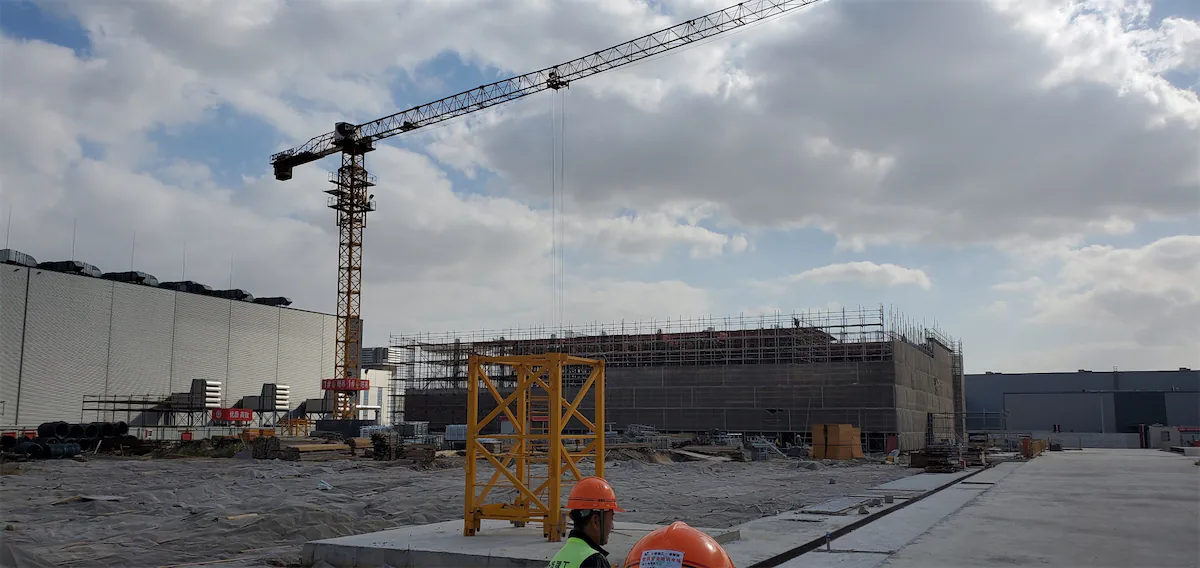
Delivery
Executing the project required meticulous coordination across multiple disciplines. BSI Engineering managed the procurement of critical components such as Siemens PLCs and SIS, High Temperature Custom Electric Heaters, and high-temperature valves. The facilities were equipped with advanced rotary traverse systems, gas analysis system, data acquisition system and high-temperature alloy designs to withstand the extreme conditions of combustor testing.
The construction process emphasized precision and quality control, with all systems rigorously tested before commissioning. Software programming for facility operation was integrated seamlessly, providing clients with a user-friendly interface for managing testing processes. The result was a pair of world-class test cells delivered on schedule and within budget.
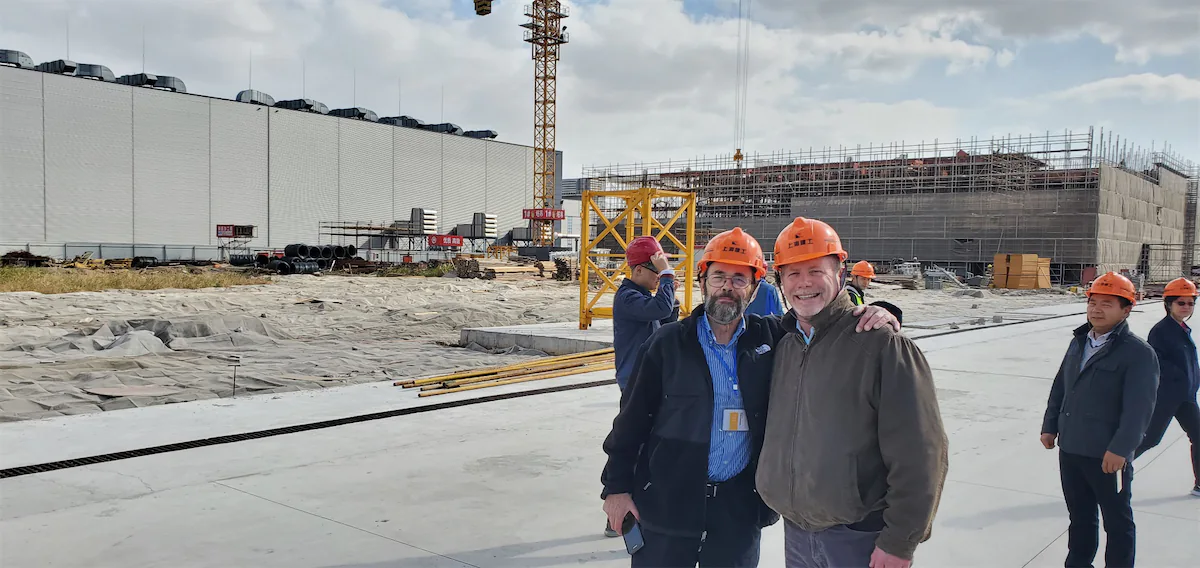
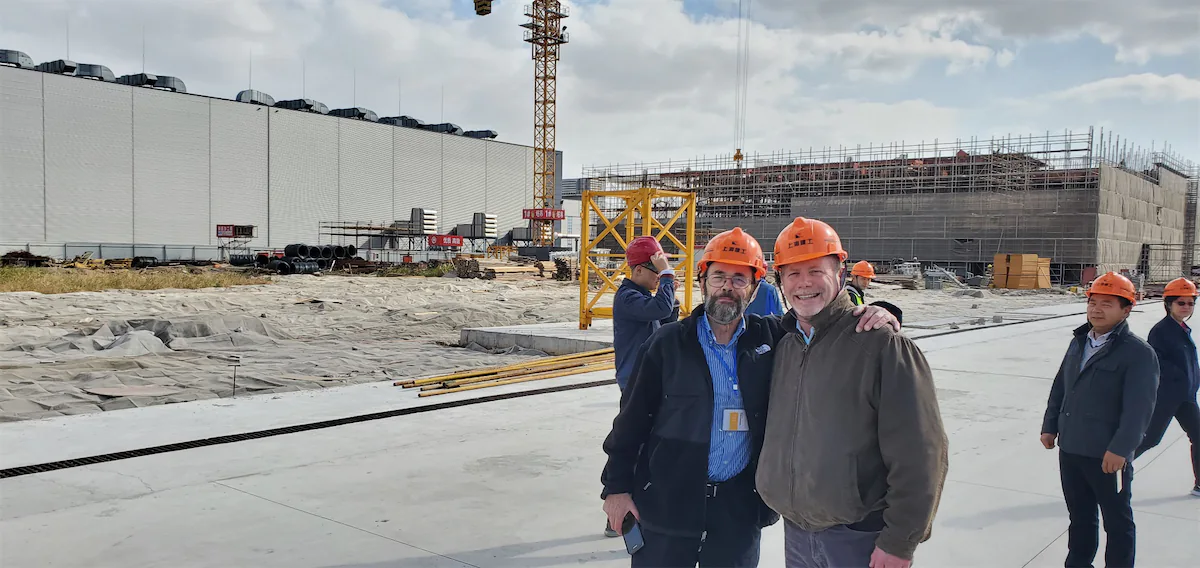
Results
Results
The completion of the combustor test cells marked a transformative milestone for the client’s operations. The new facilities allowed for a 30% increase in testing capacity, enabling the evaluation of a wider range of turbine designs. Operational efficiency saw a 25% improvement due to advanced automation and streamlined workflows.
In addition to boosting performance, the facilities achieved a 15% reduction in operational costs through optimized energy usage in heaters and compressors. These outcomes not only validated BSI Engineering's approach but also positioned the client as a leader in turbine testing capabilities.
Increase in testing capacity.
Reduction in setup times.
Improvement in data accuracy.
Other Projects
Read more success stories
Contact
Ready to transform your vision into reality?
Contact BSI Engineering today to discuss your project needs. Our team of over 250 engineers and designers across 4 Midwest offices is ready to serve you.