Case Study
Expanding Aircraft Brake Pad Manufacturing Capacity with Innovative Furnace Installations
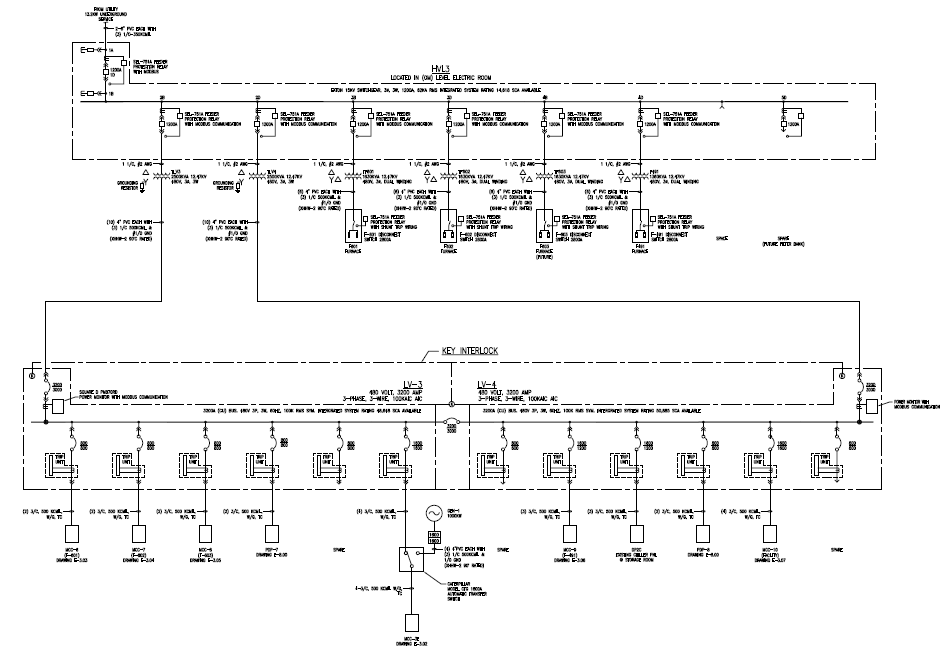
Introduction
BSI Engineering collaborated with an aircraft brake pad manufacturer to expand their production facility, addressing the growing demand for their products. The project involved constructing a two-story addition and installing eight high-performance furnaces, along with the supporting infrastructure needed for efficient operations.
This transformative project not only increased production capacity but also modernized the facility’s systems to meet current industry standards. The successful completion reinforced the client’s ability to compete in a demanding market.
Discovery
The client required a significant capacity increase to keep pace with rising demand for aircraft brake pads. Key project requirements included:
- Installing eight new furnaces in a two-story expansion.
- Upgrading electrical, lighting, and fire safety systems.
- Ensuring the facility adhered to stringent industry regulations.
Challenges included integrating the new systems seamlessly with existing infrastructure while minimizing downtime.
Research
To deliver a robust solution, BSI Engineering conducted detailed research into furnace technologies, utility systems, and structural requirements. The team assessed the client’s existing infrastructure, evaluating electrical capacity, fire safety systems, and workflow efficiency to identify gaps.
The research also included studying advanced furnace designs to ensure energy efficiency and reliability. Regulatory compliance and environmental considerations were thoroughly analyzed, ensuring the new systems met or exceeded industry standards. These findings formed the foundation for a comprehensive project plan.
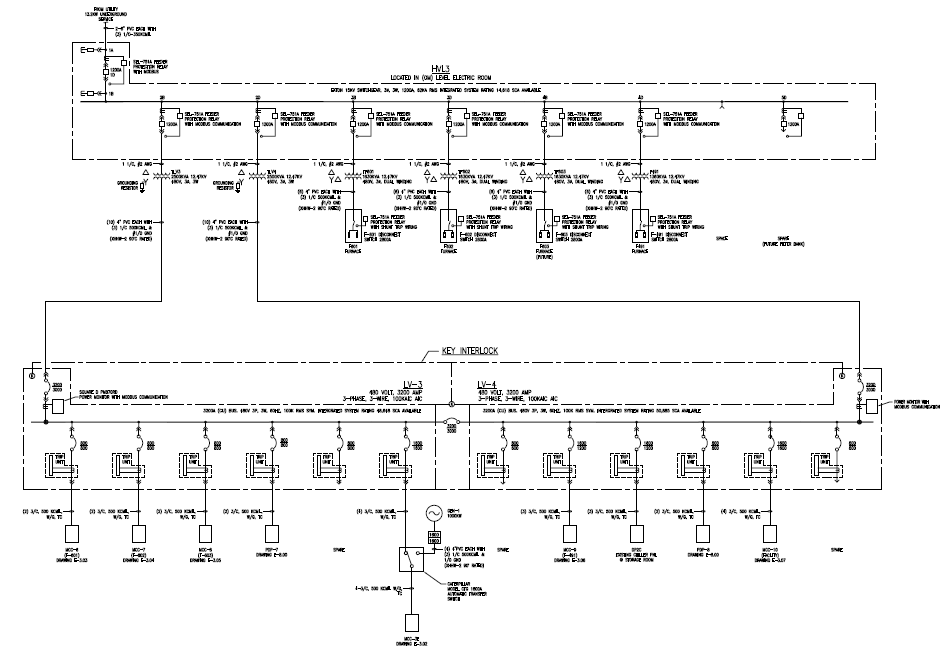
Planning
A phased approach was developed to minimize disruption during construction. The plan included the design of an 88,000-square-foot, two-story addition that would house the new furnaces and associated equipment. Utility upgrades, including a new electrical service from the utility provider, were incorporated to support the additional load.
Special attention was given to fire safety, power distribution, and communication systems to ensure seamless integration with existing operations. The layout was designed to optimize workflow, allowing for efficient movement of materials and personnel. Stakeholder input was integrated throughout the planning phase to align the project with the client’s operational goals.
Delivery
BSI Engineering successfully delivered the project by managing every phase:
- Construction: Built an 88,000-square-foot, two-story addition with furnace installations and supporting process equipment.
- Systems Integration: Designed and implemented power distribution, lighting, and communications infrastructure.
- Compliance Assurance: Ensured all new installations met industry safety and environmental standards.
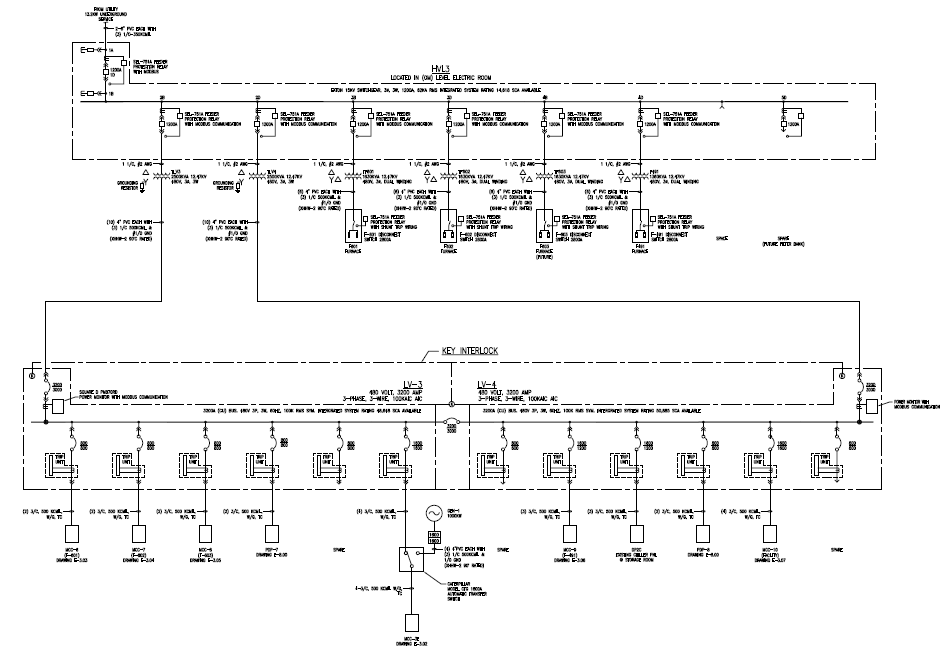
Results
Results
The expanded facility achieved a 40% increase in production capacity, enabling the manufacturer to meet rising demand for their brake pads. Energy-efficient furnaces and optimized utility systems reduced operational costs by 15%, providing long-term savings. Safety standards were also significantly improved, with modern fire alarm systems enhancing workplace security.
The successful expansion positioned the client to scale operations further in the future, solidifying their market position. The project exemplified BSI Engineering’s ability to deliver impactful solutions tailored to complex industrial challenges.
Boost in production capacity with the new furnaces.
Sq. ft. of additional space for manufacturing.
Reduction in energy costs through efficient furnace operations.
Other Projects
Read more success stories
Contact
Ready to transform your vision into reality?
Contact BSI Engineering today to discuss your project needs. Our team of over 250 engineers and designers across 4 Midwest offices is ready to serve you.